QR Code
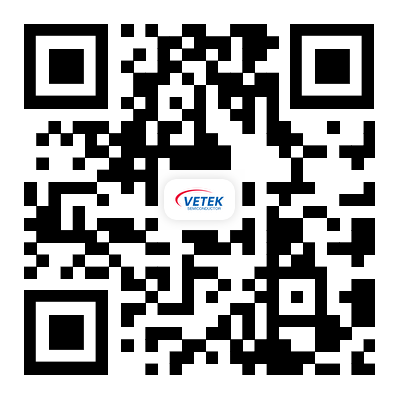
About Us
Products
Contact Us
Phone
Fax
+86-579-87223657
E-mail
Address
Wangda Road, Ziyang Street, Wuyi County, Jinhua City, Zhejiang Province, China
Address
Wangda Road, Ziyang Street, Wuyi County, Jinhua City, Zhejiang Province, China
Tel