QR Code
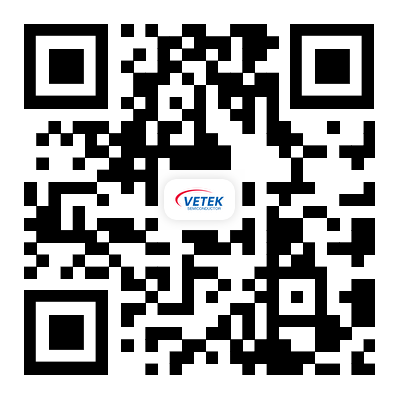
About Us
Products
Contact Us
Phone
Fax
+86-579-87223657
E-mail
Address
Wangda Road, Ziyang Street, Wuyi County, Jinhua City, Zhejiang Province, China
Silicon epitaxy is a crucial basic process in modern semiconductor manufacturing. It refers to the process of growing one or more layers of single-crystal silicon thin films with specific crystal structure, thickness, doping concentration and type on a precisely polished single-crystal silicon substrate. This grown film is called an epitaxial layer (Epitaxial Layer or Epi Layer), and a silicon wafer with an epitaxial layer is called an epitaxial silicon wafer. Its core characteristic is that the newly grown epitaxial silicon layer is a continuation of the substrate lattice structure in crystallography, maintaining the same crystal orientation as the substrate, forming a perfect single crystal structure. This allows the epitaxial layer to have precisely designed electrical properties that are different from those of the substrate, thus providing a basis for the manufacture of high-performance semiconductor devices.
Vertial Epitaxial Susceptor for Silicon Epitaxy
1) Definition: Silicon epitaxy is a technology that deposits silicon atoms on a single-crystal silicon substrate by chemical or physical methods and arranges them according to the substrate lattice structure to grow a new single-crystal silicon thin film.
2) Lattice matching: The core feature is the orderliness of epitaxial growth. The deposited silicon atoms are not randomly stacked, but are arranged according to the crystal orientation of the substrate under the guidance of the "template" provided by the atoms on the surface of the substrate, achieving atomic-level precise replication. This ensures that the epitaxial layer is a high-quality single crystal, rather than polycrystalline or amorphous.
3) Controllability: The silicon epitaxy process allows precise control of the thickness of the growth layer (from nanometers to micrometers), the doping type (N-type or P-type), and the doping concentration. This allows regions with different electrical properties to be formed on the same silicon wafer, which is the key to manufacturing complex integrated circuits.
4) Interface characteristics: An interface is formed between the epitaxial layer and the substrate. Ideally, this interface is atomically flat and contamination-free. However, the quality of the interface is critical to the performance of the epitaxial layer, and any defects or contamination may affect the final performance of the device.
Epitaxial growth of silicon mainly depends on providing the right energy and environment for silicon atoms to migrate on the surface of the substrate and find the lowest energy lattice position for combination. The most commonly used technology at present is Chemical Vapor Deposition (CVD).
Chemical Vapor Deposition (CVD): This is the mainstream method to achieve silicon epitaxy. Its basic principles are:
● Precursor transport: Gas containing silicon element (precursor), such as silane (SiH4), dichlorosilane (SiH2Cl2) or trichlorosilane (SiHCl3), and dopant gas (such as phosphine PH3 for N-type doping and diborane B2H6 for P-type doping) are mixed in precise proportions and passed into a high-temperature reaction chamber.
● Surface reaction: At high temperatures (usually between 900°C and 1200°C), these gases undergo chemical decomposition or reaction on the surface of the heated silicon substrate. For example, SiH4→Si(solid)+2H2(gas).
● Surface migration and nucleation: The silicon atoms produced by decomposition are adsorbed to the substrate surface and migrate on the surface, eventually finding the right lattice site to combine and start to form a new single crystal layer. The quality of epitaxial growth silicon depends largely on the control of this step.
● Layered growth: The newly deposited atomic layer continuously repeats the lattice structure of the substrate, grows layer by layer, and forms an epitaxial silicon layer with a specific thickness.
Key process parameters: The quality of the silicon epitaxy process is strictly controlled, and the key parameters include:
● Temperature: affects the reaction rate, surface mobility and defect formation.
● Pressure: affects gas transport and reaction path.
● Gas flow and ratio: determines the growth rate and doping concentration.
● Substrate surface cleanliness: Any contaminant may be the origin of defects.
● Other technologies: Although CVD is the mainstream, technologies such as Molecular Beam Epitaxy (MBE) can also be used for silicon epitaxy, especially in R&D or special applications that require extremely high precision control. MBE directly evaporates silicon sources in an ultra-high vacuum environment, and atomic or molecular beams are directly projected onto the substrate for growth.
Silicon epitaxy technology has greatly expanded the application range of silicon materials and is an indispensable part of the manufacturing of many advanced semiconductor devices.
● CMOS technology: In high-performance logic chips (such as CPUs and GPUs), a low-doped (P− or N−) epitaxial silicon layer is often grown on a heavily doped (P+ or N+) substrate. This epitaxial silicon wafer structure can effectively suppress the latch-up effect (Latch-up), improve device reliability, and maintain the low resistance of the substrate, which is conducive to current conduction and heat dissipation.
● Bipolar transistors (BJT) and BiCMOS: In these devices, silicon epitaxy is used to accurately construct structures such as the base or collector region, and the gain, speed and other characteristics of the transistor are optimized by controlling the doping concentration and thickness of the epitaxial layer.
● Image sensor (CIS): In some image sensor applications, epitaxial silicon wafers can improve the electrical isolation of pixels, reduce crosstalk, and optimize the photoelectric conversion efficiency. The epitaxial layer provides a cleaner and less defective active area.
● Advanced process nodes: As device size continues to shrink, the requirements for material properties are getting higher and higher. Silicon epitaxy technology, including selective epitaxial growth (SEG), is used to grow strained silicon or silicon germanium (SiGe) epitaxial layers in specific areas to improve carrier mobility and thus increase the speed of transistors.
Horizonal Epitaxial Susceptor for Silicon Epitaxy
Although silicon epitaxy technology is mature and widely used, there are still some challenges and problems in the epitaxial growth of silicon process:
● Defect control: Various crystal defects such as stacking faults, dislocations, slip lines, etc. may be generated during epitaxial growth. These defects can seriously affect the electrical performance, reliability and yield of the device. Controlling defects requires an extremely clean environment, optimized process parameters, and high-quality substrates.
● Uniformity: Achieving perfect uniformity of epitaxial layer thickness and doping concentration on large-size silicon wafers (such as 300mm) is an ongoing challenge. Non-uniformity can lead to differences in device performance on the same wafer.
● Autodoping: During the epitaxial growth process, high-concentration dopants in the substrate may enter the growing epitaxial layer through gas phase diffusion or solid-state diffusion, causing the epitaxial layer doping concentration to deviate from the expected value, especially near the interface between the epitaxial layer and the substrate. This is one of the issues that need to be addressed in the silicon epitaxy process.
● Surface morphology: The surface of the epitaxial layer must remain highly flat, and any roughness or surface defects (such as haze) will affect subsequent processes such as lithography.
● Cost: Compared with ordinary polished silicon wafers, the production of epitaxial silicon wafers adds additional process steps and equipment investment, resulting in higher costs.
● Challenges of Selective Epitaxy: In advanced processes, selective epitaxial growth (growth only in specific areas) places higher demands on process control, such as selectivity of growth rate, control of lateral overgrowth, etc.
As a key semiconductor material preparation technology, the core feature of silicon epitaxy is the ability to accurately grow high-quality single-crystal epitaxial silicon layers with specific electrical and physical properties on single-crystal silicon substrates. Through precise control of parameters such as temperature, pressure, and airflow in the silicon epitaxy process, the layer thickness and doping distribution can be customized to meet the needs of various semiconductor applications such as CMOS, power devices, and sensors.
Although epitaxial growth of silicon faces challenges such as defect control, uniformity, self-doping, and cost, with the continuous advancement of technology, silicon epitaxy is still one of the core driving forces for promoting performance improvement and functional innovation of semiconductor devices, and its position in epitaxial silicon wafer manufacturing is irreplaceable.
+86-579-87223657
Wangda Road, Ziyang Street, Wuyi County, Jinhua City, Zhejiang Province, China
Copyright © 2024 VeTek Semiconductor Technology Co., Ltd. All Rights Reserved.
Links | Sitemap | RSS | XML | Privacy Policy |