QR Code
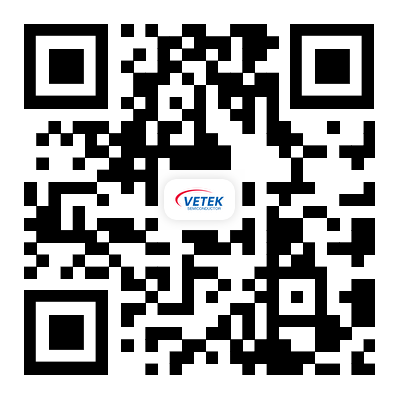
About Us
Products
Contact Us
Phone
Fax
+86-579-87223657
E-mail
Address
Wangda Road, Ziyang Street, Wuyi County, Jinhua City, Zhejiang Province, China
Porous silicon carbide ceramic plate is a porous structure ceramic material made of silicon carbide (SiC) by special processes (such as foaming, 3D printing or adding pore-forming agents). Its core features include:
● Controllable porosity: 30%-70% adjustable to meet the needs of different application scenarios.
● Uniform pore size distribution: ensure gas/liquid transmission stability.
● Lightweight design: reduce equipment energy consumption and improve operating efficiency.
1. High temperature resistance and thermal management (mainly to solve the problem of equipment thermal failure)
● Extreme temperature resistance: continuous working temperature reaches 1600°C (30% higher than alumina ceramics).
● High efficiency thermal conductivity: thermal conductivity coefficient is 120 W/(m·K), fast heat dissipation protects sensitive components.
● Ultra-low thermal expansion: thermal expansion coefficient is only 4.0×10⁻⁶/°C, suitable for operation under extreme high temperature, effectively avoiding high temperature deformation.
2. Chemical stability (reducing maintenance costs in corrosive environments)
● Resistant to strong acids and alkalis: can withstand corrosive media such as HF and H₂SO₄
● Resistant to plasma erosion: life in dry etching equipment is increased by more than 3 times
3. Mechanical strength (extending equipment life)
● High hardness: Mohs hardness is as high as 9.2, and wear resistance is better than stainless steel
● Bending strength: 300-400 MPa, supporting wafers without warping
4. Functionalization of porous structures (improving process yield)
● Uniform gas distribution: CVD process film uniformity is increased to 98%.
● Precise adsorption control: The positioning accuracy of the electrostatic chuck (ESC) is ±0.01mm.
5. Cleanliness guarantee (in compliance with semiconductor-grade standards)
● Zero metal contamination: purity > 99.99%, avoiding wafer contamination
● Self-cleaning characteristics: microporous structure reduces particle deposition
Scenario 1: High-temperature process equipment (diffusion furnace/annealing furnace)
● User pain point: Traditional materials are easily deformed, resulting in wafer scrapping
● Solution: As a carrier plate, it operates stably under 1200°C environment
● Data comparison: The thermal deformation is 80% lower than that of alumina
Scenario 2: Chemical vapor deposition (CVD)
● User pain point: Uneven gas distribution affects film quality
● Solution: The porous structure makes the reaction gas diffusion uniformity reach 95%
● Industry case: Applied to 3D NAND flash memory thin film deposition
Scenario 3: Dry etching equipment
● User pain point: Plasma erosion shortens component life
● Solution: Anti-plasma performance extends the maintenance cycle to 12 months
● Cost-effectiveness: equipment downtime is reduced by 40%
Scenario 4: Wafer cleaning system
● User pain point: frequent replacement of parts due to acid and alkali corrosion
● Solution: HF acid resistance makes the service life reach more than 5 years
● Verification data: strength retention rate >90% after 1000 cleaning cycles
Comparison dimensions |
Porous SiC ceramic plate |
Alumina ceramic |
Graphite material |
Temperature limit |
1600°C (no oxidation risk) |
1500°C is easy to soften |
3000°C but requires inert gas protection |
Maintenance cost |
Annual maintenance cost reduced by 35% |
Quarterly replacement required |
Frequent cleaning of dust generated |
Process compatibility |
Supports advanced processes below 7nm |
Only applicable to mature processes |
Applications limited by pollution risk |
Q1: Is porous SiC ceramic plate suitable for gallium nitride (GaN) device production?
Answer: Yes, its high temperature resistance and high thermal conductivity are particularly suitable for GaN epitaxial growth process and have been applied to 5G base station chip manufacturing.
Q2: How to choose the porosity parameter?
Answer: Choose according to the application scenario:
● Gas distribution: 40%-50% open porosity is recommended
● Vacuum adsorption: 60%-70% high porosity is recommended
Q3: What is the difference with other silicon carbide ceramics?
Answer: Compared with dense SiC ceramics, porous structures have the following advantages:
● 50% weight reduction
● 20 times increase in specific surface area
● 30% reduction in thermal stress
+86-579-87223657
Wangda Road, Ziyang Street, Wuyi County, Jinhua City, Zhejiang Province, China
Copyright © 2024 VeTek Semiconductor Technology Co., Ltd. All Rights Reserved.
Links | Sitemap | RSS | XML | Privacy Policy |